When it comes to producing charcoal or biochar, choosing the right carbonization furnace is crucial for efficiency and profitability. Two popular options are the batch carbonization furnace and the continuous carbonization furnace. Each has its own strengths and ideal use cases. In this blog, we will compare these two types of furnaces, focusing on their features, benefits, and applications. By the end, you’ll know which furnace is the best fit for your needs.
What is a Batch Carbonization Furnace?
Batch carbonization furnace is also a common hoisting furnace. The raw materials are first loaded into the carbonization furnace, and then the carbonization furnace is heated for carbonization. After carbonization, they are discharged from the furnace. It can carbonize relatively large solid raw materials such as logs and sticks. The carbonization time is generally 6-8 hours. After carbonization is completed, it is cooled and taken out of the furnace.
Batch Carbonization Furnace Features
Lower Initial Cost: More affordable for small-scale operations.
Flexibility: Can handle different types of biomass in separate batches.
Precision: Offers better control over temperature and carbonization time.
Batch furnaces are ideal for small businesses or those with varying production needs.
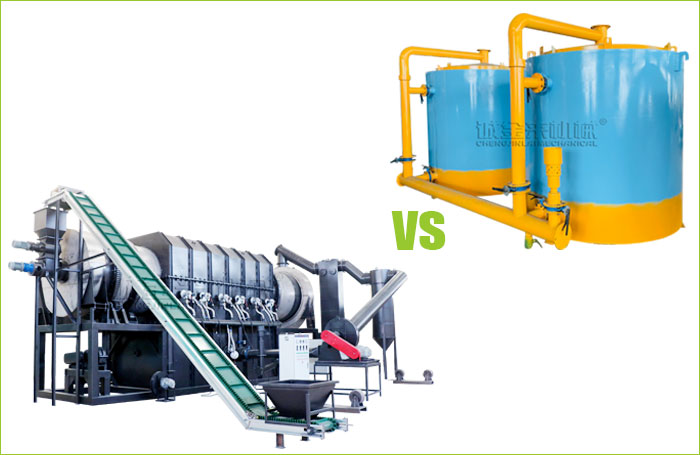
What Is A Continuous Carbonization Furnace?
The continuous carbonization furnace machine can run continuously for 24 hours, with continuous feeding and continuous carbonization. It is designed for mass production, and the material passes through the furnace through a conveyor belt or similar system. The furnace maintains a constant temperature to ensure consistent results.
The continuous carbonization machine first heats the carbonization furnace, and then starts feeding from the feed port after reaching the carbonization temperature. The raw materials are not pre-loaded into the furnace.
The raw materials enter the carbonization furnace continuously when the equipment is running, so the sealing of the feed port must be ensured to ensure oxygen-free carbonization in the main furnace, so branches, logs, etc. need to be crushed, and the size cannot be too large, generally requiring less than 2 cm. It is particularly suitable for the carbonization of sawdust, rice husks, straw husks, etc.
After the raw materials enter the carbonization furnace, they move with the rotation of the carbonization furnace, slowly moving from the feed port to the carbon outlet. The specific time can be set, generally about 30 minutes. When the raw materials move to the carbon outlet, carbonization is basically completed, and then carbon is discharged from the carbon outlet.
Continuous Carbonization Furnace Features
High efficiency: uninterrupted processing of large amounts of biomass.
Consistency: Due to stable temperature, uniform quality charcoal can be produced.
Low labor cost: minimal human intervention is required, thereby reducing operating expenses.
Batch Carbonization Furnace Vs Continuous Carbonization Furnace
There are significant differences between continuous carbonization furnaces and batch carbonization furnaces in many aspects. The following is a detailed description of the points and summaries:
Working principle:
Continuous carbonization furnace: Using a continuous carbonization process, the material continuously enters the carbonization chamber through the feed system, is carbonized by the high temperature of the heating system, and is continuously discharged through the discharge system. During the whole process, carbonization, purification, cooling and other steps work together to form a continuous production line.
Batch carbonization furnace: A batch-by-batch carbonization method is used. After each carbonization process is completed, the furnace needs to be cooled, cleaned, and reloaded with raw materials before the next carbonization process begins. The carbonization process and the cooling process are carried out separately.
Production efficiency:
Continuous carbonization furnace: Due to the continuous production method, the production efficiency is high and the carbonized products can be provided continuously and stably.
Batch carbonization furnace: Due to the need to carbonize batch by batch, the production efficiency is relatively low, which is suitable for small-scale production or laboratory research.
Degree of automation:
Continuous carbonization furnace: Equipped with advanced automatic control system to realize the control of carbonization process, reduce the difficulty of operation and improve carbonization efficiency.
Batch carbonization furnace: The degree of automation is relatively low, the operation is more cumbersome, and manual cooling, cleaning and loading of raw materials are required.
Scope of application:
Continuous carbonization furnace: Suitable for large-scale and continuous production, widely used in biomass energy utilization, charcoal production and other fields.It is suitable for large-scale converting biomass materials such as wood, coconut shells or rice husks into charcoal.
Batch carbonization furnace: Suitable for small-scale, batch production or laboratory research, such as sample preparation, small-scale production, etc.
Environmental protection:
Continuous carbonization furnace: Through advanced energy recovery technology and purification system, it can minimize energy waste and environmental pollution, which is in line with the modern green environmental protection concept.
Batch carbonization furnace: It is relatively weak in environmental protection, and additional environmental protection measures may be required to reduce exhaust gas emissions and environmental pollution.
Equipment structure:
Continuous carbonization furnace: It has a compact structure and a small footprint. It includes multiple parts such as gasification system, purification system, carbonization system and control system, which work together to complete the carbonization process.
Batch carbonization furnace: The structure is relatively simple, usually there is only one carbonization area, and manual cooling, cleaning and loading of raw materials are required for the furnace.
Carbonization Furnaces Maintenance Tips
To ensure your furnace operates efficiently, follow these maintenance tips:
- Regular Cleaning: Remove dust and debris to prevent clogging and wear.
- Inspection: Check for signs of wear or damage, especially in heating elements and seals.
- Lubrication: Keep moving parts well-lubricated to reduce friction and extend lifespan.
Proper maintenance ensures long-term performance and reduces repair costs.
Conclusion
In general, continuous carbonization furnaces are more suitable for large-scale industrial production, especially when there are high requirements for output and product consistency. Batch carbonization furnaces also called vertical carbonization furnace are more suitable for small-scale production, especially when the initial investment budget is limited. The choice of carbonization furnace depends on the specific production needs, budget and the characteristics of the materials being processed.
By understanding the features, benefits, and applications of each type, you can choose the furnace that best meets your needs. Whether you prioritize flexibility, efficiency, or cost-effectiveness, the right furnace can significantly enhance your production process.